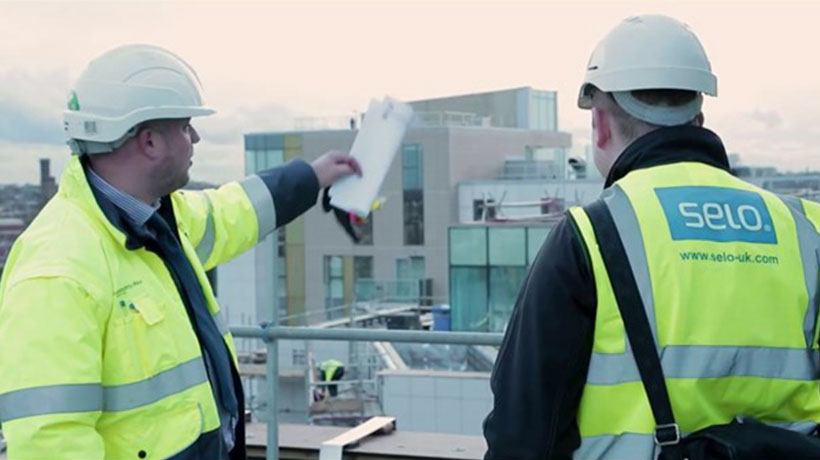
Managing a construction project is a fine art, often a stressful juggling between competing factors. The client wants a high standard but the budget is tight. The building must be signed off by a certain date but work must be conducted safely and completed to building code standards.
At the end of the day, the desired outcome is delivering a project safely, on time, on budget and to a high spec, whilst fully complying (at the very least) with all relevant safety legislation. But there are several key factors that can make the difference between a successful project and a troublesome one. How important is it to run a risk-free construction project?
Fire risk
Fire risk is always a concern on any construction project. One of the main elements of an effective fire strategy is containing and controlling fire through compartmentation. Buildings have been designed with compartmentation built-in for years, but it is only effective if the elements that work together to form that compartment are fully compliant.
Fire resistance compliance is essential to life safety
Fire compartmentation within a building is a life safety system, and all components of that system must comply with their own specific product requirements as well as those of the other elements of that system. Fire doors are clearly a significant part of compartmentation. Failing to ‘get it right’ on fire doors, whether it’s badly fitted intumescent or using insufficiently powered door closers, can lead to loss of life because the compartmentation within the building fails to contain the fire.
Loss of life due to non-compliant products being fitted, either to meet cost/time constraints or just ignorance as to the requirements of the particular building as a system, is clearly unacceptable. It also doesn’t make any sense from a practical business perspective as it can lead to delays and add unscheduled costs to a building project.
The knock-on effect of failed inspections
Failed inspections due to either products not demonstrating the correct performance requirements, or not being suitably tested for use in the specified and built system of compartmentation, inevitably lead to delays and chargeable remedial work. Frequently, inspections are not carried out until the building has passed second fix stage and decorating/finishing works are being completed. Failing inspections at this stage results in work that has already been signed off being stripped right back to basics.
This doesn’t just affect the door installer – having to rip out and re-do entire doorsets has a knock-on effect on a variety of trades – plasterers, electricians and decorators, for example – many of whom will have moved onto other projects. Not getting it right can create delays and costly disputes over responsibility for the additional works. Failed inspections can be avoided entirely if time is spent getting the specification right at the outset.
Getting the specification right
Doorsets can fail on paper, before they are even installed, if they are incorrectly specified at the outset or the main contractor has gone ahead and ordered something they have used before without checking the specification. The consequences can be costly, both in terms of life safety and in terms of time and budget.
A good door manufacturer should be keen to get involved in a project at an early point so that they can give the benefit of their experience and expertise, from concept stage through to assisting with design, compliance and installation. It will allow a smoother transition from concept though to execution, making sure all parties involved are aware of all risks and opportunities. This gives all stakeholders in the project a much better experience, and the end result is a better building outcome and a much lower risk of failing to protect life.
And as well as helping to protect life safety, it is always cheaper and quicker to do it right the first time rather than having to deal with issues, remakes and/or remedial works.
Understanding complex builds
Choosing a project partner with experience of complex construction projects, and engaging that partner as early as possible in the process, significantly increases the chances of getting everything right first time. Aside from supplying a technically excellent product, the project partner must have an appreciation of the detailed, interlinked scheduling and managing risk must be uppermost in everyone’s mind throughout the project. At Selo, we have many years of experience on large and diverse projects so we know that if one part fails, the whole system fails.
Halo Assist – support that surrounds every project
When we are part of a project, we care deeply about its success and we always aim above and beyond the minimum standards. That is why we have developed our own project support framework, Halo Assist, which provides detailed assistance at every phase of the project. At concept stage, we check drawings and specifications, ensuring that design aspirations can be achieved alongside compliance requirements. We spend time securing compliance certification, carrying out site visits and confirming cost schedules to ensure that every detail is accounted for. A dedicated Project Manager will oversee successful production, delivery and installation, and a site technician will carry out an installation demo, supporting your team on site to ensure they get it right first time.
In an industry where discrepancy or failure can have significant logistical, cost or legal implications, we are committed to reducing every element of risk that we can so that our customers can use us with confidence.